Handmade English Leather Goods | Made to Last by Barnes & Moore

It is no secret that many fashion houses have been substituting quality for profit for some time, although it is not just the fashion industry that has been passing off cheaper goods to their customers. The pressure is on to make more profits and the simplest way to achieve that is to reduce the cost-of-sales by using inferior quality materials or by spending less on the manufacturing build. This week in the news, even our beloved Toblerone chocolate is changing its iconic shape to reduce the weight from 400g to 360g. Everywhere I look there are examples of not getting value for money anymore. However ultimately the consumer has the power, you make a choice on what to buy and it seems that consumers have had enough of being puppets to the super brands and wanting to know where their products come from and how they are made.
I’m no different and when buying clothing, I always like to know exactly where the materials come from, where the clothing is made and conditions of the workers – all very important questions.
A few months ago, I was introduced to the brand Barnes & Moore and it was completely refreshing in the way they conduct business and the passion they have for their products. When a brand can talk about every single aspect of their manufacturing process from start to finish and explains in detail what exactly makes their products better than the competition, you cant help admire what they are doing and I wanted to buy into this exceptional attention to detail.
Barnes & Moore select the best hides from some of the best tanneries in the world and then hand cut the belt strip to the required length. The belt strip’s then buffed, to remove the protective wax on the surface, and cut to suit the relevant waist size. The tips are then cut, and the edges bevelled, dyed and hand ‘burnished’. The burnishing process involves waxing the edge and using friction to flatten the leather fibres, which allows the belt to pass more easily through belt loops. Many commercial manufacturers replace this process with painting the edges instead, as it’s labour intensive, and time consuming, so it’s only generally found on higher end products.
It doesn’t stop there, a belt in not complete without a suitable buckle. Barnes & Moore then select a buckle for the belt, their Garrison buckle is cast in sand, by hand, at England’s last remaining sand cast foundry, and is solid brass, and either polished, or dull nickel plated. The buckles are riveted in place with solid brass rivets, (80% of rivets on belts are cheaper, base metal rivets), and the solid brass keeper secured. The belt holes are punched by hand, and the belt is finally polished before being boxed. Barnes & Moore then add a miniature pot of their hand made wax (contains natural mineral oil, beeswax, and natural vanilla. no chemicals) and ship it out to you lucky people!
Of course, I have just chosen to explain to you about their belt manufacturing process, although in typical Barnes & Moore style, you can find further information on their website with regards to the manufacturing process of each product.
I’ve had my Barnes & Moore products for about 3 months now. I tend to wear them for outdoor types of activities like walking my dog, going for walks to a warm country pub or weekend breaks away – I think it is because their products are so hardy. My favourite product of theirs that I have is this Despatch Messenger Bag in Olive because it was pristine when I received it, yet the more I use it, the better the leather looks - it gains a whole new look and personality. It’s a bit like leather sofas, which always look better and better after every year of age.
SHOP BARNES & MOORE
Photography by Rebecca Spencer
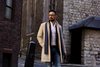
Founder of this eponymous blog, focusing on men's fashion & lifestyle.